How a Cardboard Baler Can Save Time, Money, and Resources
Businesses take great pride and responsibility for their efforts to minimize their environmental impact. One of the most effective ways to reduce waste and promote sustainability is through recycling. A cardboard baler is an essential tool for any business looking to improve its recycling practices.
In this guide, we will explore everything you need to know about balers, including the different types available, their benefits, and how to choose the right one for your business.
Cardboard Balers for Sale near Grand Rapids, Michigan
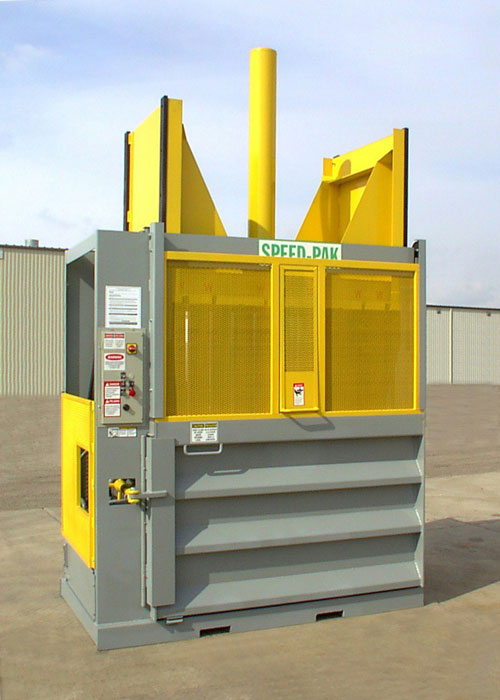
Why Your Company Needs A Cardboard Baler
As a business owner, you understand the importance of recycling and the positive impact it has on the environment. However, managing your cardboard waste can be challenging, especially if you have a high volume of cardboard waste. This is where a cardboard baler comes in handy.
Cardboard balers are efficient machines designed specifically to compress cardboard into compact bales. These bales can then be easily transported and recycled, reducing the space required for storage and disposal. By investing in a cardboard baler, you can improve your recycling practices and make a meaningful impact on the environment.
Cardboard and plastic balers are commonly referred to as cardboard smashers, retail balers, cardboard balers, or simply cardboard compactors. These machines come in various types and sizes to meet different business needs.
Types of Balers
When it comes to cardboard balers, there are several variations available on the market. Two of the most common types are the vertical baler and the horizontal baler.
Vertical balers are designed to handle small to medium volumes of cardboard waste and are perfect for businesses with limited space. They are easy to operate and can be used to bale a wide range of materials, including cardboard, paper, and plastic. Vertical balers are also more affordable than other types of balers, making them an excellent choice for small businesses.
On the other hand, horizontal balers are suitable for large-scale recycling and are commonly used in industrial settings. They are designed to handle large volumes of waste and can be used to bale materials like cardboard, paper, and plastics. Horizontal balers are more expensive than vertical balers, but they are more efficient and can handle larger volumes of waste.
When choosing a cardboard baler, it’s essential to consider your business’s needs and budget. If you have limited space and generate small to medium volumes of waste, a vertical baler may be the best choice for you. However, if you’re an industrial business with high volumes of waste, a horizontal baler may be the better option.
Vertical Baler
Horizontal Baler
Benefits of Using a Cardboard Baler
One of the primary benefits of using a cardboard baler is the space-saving advantage it offers. By compacting cardboard waste into bales, you can significantly reduce the amount of space needed for waste disposal. This is especially beneficial for businesses that generate a lot of cardboard waste, such as retailers, warehouses, and manufacturing facilities. A cardboard baler allows you to optimize your workspace, reduce the need for large dumpsters, and create a more efficient and organized waste management process. The benefits of using a cardboard baler don’t end there. Recycling cardboard also helps in reducing your carbon footprint and promoting sustainability. It conserves natural resources and reduces the amount of waste that ends up in landfills, which can take hundreds of years to decompose. Additionally, recycling cardboard decreases carbon emissions by reducing the demand for virgin materials and the energy needed to produce new products.
Moreover, using a cardboard baler can enhance workplace safety. When cardboard boxes and other packaging materials pile up, it can create a cluttered and potentially hazardous environment. By quickly and safely compressing your cardboard waste with a baler, you can reduce clutter and minimize the risk of accidents and injuries. This not only encourages a safer work environment but also helps businesses avoid costly workplace injuries and insurance claims. Furthermore, a baler can save businesses money on trash removal fees. By reducing the volume of cardboard waste, businesses can reduce the frequency of trash pickups and avoid overfilling dumpsters. This not only saves money but also reduces the amount of waste that ends up in landfills.
How to Choose the Right Cardboard Baler
Selecting the right baler for your business can be challenging, but considering several factors can make the process easier. One of the most important factors is the size of your business and the amount of cardboard waste produced. You’ll also need to assess the space available for the machine, your budget, and the required features, such as automatic or manual operation.
Maintaining Your Cardboard Baler
Once you’ve chosen and installed your baler, it’s important to keep it in good working condition. This involves performing regular maintenance and inspections to ensure the machine is functioning properly. Maintenance includes checking and replacing hydraulic fluids, inspecting and lubricating moving parts, and cleaning the machine to prevent buildup.
Did you know Cardboard is the single largest component of waste that businesses produce annually? Learn more about cardboard recycling by reading this article from the Wastecare Corporation.